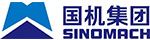
8Cr4Mo4V鋼是我國應用較為廣泛的一種高溫軸承鋼,主要用于航空發動機主軸軸承的制造。隨著發動機主軸軸承的服役工況愈發惡劣,對材料性能的要求也越來越高,國內外學者開展了大量8Cr4Mo4V鋼性能提升的研究工作。作者介紹了8Cr4Mo4V鋼化學成分優化的研究進展;重點分析了8Cr4Mo4V鋼熱處理技術發展,包括傳統淬回火、貝氏體等溫淬火及尺寸穩定化等熱處理工藝;介紹了8Cr4Mo4V鋼表面強化技術的研究進展及相關成果,涉及表面合金化、涂層沉積、噴丸強化及復合強化技術;最后,結合8Cr4Mo4V鋼服役需求及相關技術研究現狀對其后續研究方向進行了展望。
軸承作為航空發動機的關鍵部件,主要作用是減小發動機各部件之間的摩擦力,傳輸載荷及保持各部件的準確位置,航空發動機主軸軸承服役環境較為惡劣,其性能直接影響發動機的運行和使用壽命,故航空發動機主軸軸承材料的選擇尤為重要。
8Cr4Mo4V(Cr4Mo4V,G80Cr4Mo4V,M50)鋼是一種典型的鉬系高速鋼,其主要合金元素除Mo外還包括大量Cr及V。傳統工藝熱處理后8Cr4Mo4V鋼中存在大量的合金碳化物,保證了其高溫硬度及耐磨性?;?Cr4Mo4V鋼優異的力學性能,20世紀80年代中期,美國宇航局開始將其應用于航空軸承。到目前為止,8Cr4Mo4V鋼依然是我國應用較為廣泛的一種高溫(使用溫度不大于316 ℃)軸承鋼,主要用于發動機主軸軸承的制造。
為進一步提高8Cr4Mo4V鋼的性能,近些年國內外學者進行了大量的研究。2020年最新報道顯示,國外學者為提高8Cr4Mo4V鋼的干摩擦性能,利用放電等離子燒結(Spark Plasma Sintering,SPS)將固體潤滑劑(SnS/ZnO)直接加到8Cr4Mo4V鋼基體中。
1、8Cr4Mo4V鋼化學成分及優化
傳統8Cr4Mo4V鋼的化學成分見表1,其中質量分數為0.75%~0.85%的C為材料提供了優異的淬透性和硬度。Cr,Mo及V均是強碳化物形成元素,可顯著提高材料的耐磨性,其中Cr在8Cr4Mo4V鋼中通常以M23C6形式存在,而Mo及V元素主要以M2C和MC形式存在。
表1 8Cr4Mo4V鋼化學成分的質量分數 %
文獻[7]對8Cr4Mo4V鋼失效模式進行了研究,指出其疲勞剝落通常起源于粗大、形狀不規則的碳化物。8Cr4Mo4V鋼中存在的大塊狀碳化物有2種:Mo為主的M2C和以無規則塊狀存在的部分MC。為消除無規則塊狀碳化物,文獻[9]通過熱力學計算重新設計了8Cr4Mo4V鋼成分(表1中的改進型)并進行了試制,結果表明:通過適當提高Cr含量,同時降低V含量,可使M2C型碳化物尺寸降至5.3 μm以下,球狀碳化物M23C6增多;經淬回火處理后改進型8Cr4Mo4V鋼的室溫硬度不低于64 HRC,400 ℃高溫下硬度不低于60 HRC,符合高溫軸承的服役要求。由于目前缺乏相關驗證,未見到該成分8Cr4Mo4V鋼的實際工程應用。
文獻[10]研究了Mg對8Cr4Mo4V鋼碳化物的影響,結果表明添加少量Mg可改善鋼的結晶組織,優化鋼錠鑄態組織中的網狀碳化物。
熱處理是決定材料最終性能的關鍵步驟,為提高8Cr4Mo4V鋼性能,研究熱處理工藝的改進技術具有重要意義。
2.1 傳統熱處理技術及其組織性能
國內外8Cr4Mo4V鋼傳統熱處理工藝均為淬火加三次回火,如圖1所示,區別在于國外淬火升溫過程為一步預熱(圖1a紅線)或三步預熱(圖1a黑色虛線),而國內基本采用一步預熱(圖1b);國外淬火冷卻過程采用分級淬火方式,主要目的是減小熱處理變形,而國內采用吹N2連續冷卻。
圖1 8Cr4Mo4V鋼國內外熱處理工藝
Fig.1 Domestic and international heat treatment process of 8Cr4Mo4V steel
淬回火工藝處理后8Cr4Mo4V鋼微觀組織及物相如圖2所示:淬火后8Cr4Mo4V鋼的晶粒較為均勻、細小,回火后8Cr4Mo4V鋼由回火馬氏體、少量殘余奧氏體(體積分數不大于3%)及碳化物組成;回火后存在無規則塊狀和彌散分布小顆粒狀碳化物,其中塊狀碳化物為淬火未溶解碳化物和回火析出碳化物。
圖2 淬回火工藝處理后8Cr4Mo4V鋼微觀組織
Fig.2 Microstructure of 8Cr4Mo4V steel after quenching and tempering process
由文獻[8]可知,淬火未溶解碳化物的主要類型為M2C和MC,而回火析出碳化物主要類型為M23C6和M2C。通常,回火析出碳化物尺寸為納米級,呈片狀或球狀,可起到二次硬化效果。然而,較早研究中受分析測試手段限制,只能從二維角度對8Cr4Mo4V鋼中碳化物進行觀察分析,制樣以及觀察方式均可能導致對其真實形狀及尺寸存在誤判。隨著三維原子探針技術的開發及應用,文獻[14]將其用于8Cr4Mo4V鋼中碳化物分析,結果如圖3所示,圖3b和圖3c為圖3a旋轉一定角度的局部放大,回火過程中析出的M2C三維形貌呈細柱狀,且連續彌散。
圖3 8Cr4Mo4V鋼中碳化物三維形貌特征.
Fig.3 Three - dimensional morphology characteristics of car-bides in 8Cr4Mo4V steel
傳統淬回火工藝處理后,8Cr4Mo4V鋼的微觀組織主要包括回火馬氏體、極少量殘余奧氏體和彌散分布的二次碳化物,室溫硬度為60~64 HRC,高溫(316 ℃ )硬度可以達到58 HRC,滿足大多數主軸軸承服役需求。
2.2 貝氏體等溫淬火強韌化工藝
當dn值超過2.0x106 mm.r/min時,韌性不足成為限制8Cr4Mo4V鋼使用的主要原因。文獻[15-16]相繼開展了強韌化技術在8Cr4Mo4V鋼熱處理工藝中的應用,以達到提高其綜合性能和軸承壽命的目的。
金屬材料通過等溫淬火獲得的下貝氏體具有優異的強度和韌性,因此等溫淬火是目前較為常用的一種金屬增韌工藝。鑒于貝氏體優異的力學性能,文獻[24-25]開展了8Cr4Mo4V鋼貝氏體等溫淬火工藝研究,以進一步提高材料的強韌性。圖4a為貝氏體等溫淬火工藝處理后8Cr4Mo4V鋼的微觀組織,圖4b為貝氏體等溫淬火工藝與常規淬回火工藝的對比,貝氏體等溫淬火工藝可以顯著提高沖擊韌性,提高幅度可達20%~50%。
圖4 貝氏體等溫淬火后8Cr4Mo4V鋼微觀組織及性能
Fig.4 Microstructure and properties of 8Cr4Mo4V steel after bainitic austempering
2.3 尺寸穩定化熱處理工藝
航空軸承除對力學性能具有較高要求外,還要求其具有優異的尺寸穩定性。8Cr4Mo4V 鋼經熱處理后盡管殘余奧氏體含量(體積分數,下同)已降至3%以下,但在存放和使用過程中依然可能進一步向馬氏體轉變,從而引起尺寸變化;殘余應力的釋放也會引起軸承尺寸變化。因此,文獻[26]開展了尺寸穩定化熱處理工藝對8Cr4Mo4V鋼微觀組織及尺寸變化的影響,即在軸承正常熱處理工序與最終冷加工工序之間增加一個穩定化熱處理工序。
8Cr4Mo4V鋼穩定化熱處理工藝如圖5所示,可以看出該工藝包括3個循環,每個循環由冷處理和中溫時效2個過程組成。
圖5 8Cr4Mo4V鋼尺寸穩定化熱處理工藝
Fig.5 Dimensional stabilization heat treatment process of 8Cr4Mo4V steel
經不同循環次數的穩定化熱處理后,8Cr4Mo4V鋼( φ30 mm×20 mm)的殘余奧氏體含量及尺寸變化結果如圖6所示。由圖6a可知:正常熱處理后殘余奧氏體含量為2.61%,隨著尺寸穩定化循環次數的增加,殘余奧氏體含量逐漸減少,經3次循環后降低至0.76%。一次穩定處理過程中馬氏體析出與殘余奧氏體轉變同時進行,8Cr4Mo4V鋼尺寸整體呈收縮現象(圖6b),說明起主要作用的因素為馬氏體析出;二次及三次穩定處理時,由于馬氏體析出反應基本完成,殘余奧氏體向馬氏體轉變成為引起尺寸變化的主要因素,因此呈現膨脹現象,且隨著循環次數的增加,殘余奧氏體含量降低,尺寸膨脹量也隨之減小。由圖6b可知,經三次循環處理后,8Cr4Mo4V鋼試樣長度平均增加1.5X10-5 mm,變化率為7.5x10-7。
圖6 尺寸穩定化熱處理循環次數對8Cr4Mo4V鋼
殘余奧氏體含量及長度的影響
Fig.6 Influence of dimensional stabilization heat treatment cycles on content of residual austenite and length of 8Cr4Mo4V steel
目前,尺寸穩定化熱處理缺乏對比試驗,后續需開展該工藝對8Cr4Mo4V鋼軸承存放或使用過程中尺寸變化的影響研究,以驗證該工藝的有效性。
(未完待續)
來源:《軸承》2021年8期
引文格式:周麗娜,楊曉峰,劉明,等.8Cr4Mo4V高溫軸承鋼熱處理及表面改性技術的研究進展[J].軸承,2021(8):1-10.
軸研所公眾號 軸承雜志社公眾號
營銷熱線
0379-64367521
0379-64880626
13693806700
0379-64880057
0379-64881181